Welcome to My Blog!
Before we dive into the content, I’d love for you to join me on my social media platforms where I share more insights, engage with the community, and post updates. Here’s how you can connect with me:
Facebook:https://www.facebook.com/profile.php?id=61563865935136
Now, let’s get started on our journey together. I hope you find the content here insightful, engaging, and valuable.
Introduction
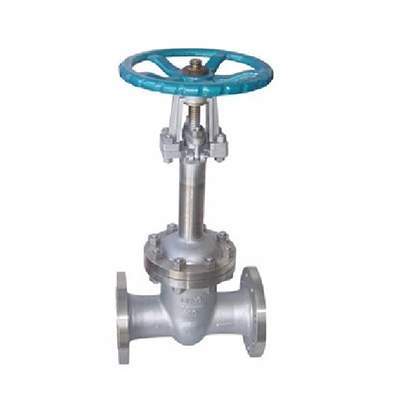
Gate valves are essential components in various industrial applications, controlling the flow of liquids or gases. The gate valve seal plays a crucial role in ensuring the valve’s efficient and leak-free operation. A well-functioning seal prevents media leakage, safeguarding system integrity and preventing costly downtime. This comprehensive guide delves into the intricacies of gate valve seals, covering their types, materials, applications, and maintenance. Understanding the importance of a properly functioning seal is paramount for maintaining system efficiency and preventing environmental hazards.
Types of Gate Valve Seals: Selecting the Right Seal for Your Application
Gate valve seals come in various types, each designed to meet specific application requirements. Understanding these different types is crucial for selecting the optimal seal for your needs. Choosing the correct seal type can significantly impact the valve’s performance and longevity. Factors like pressure, temperature, and the nature of the media being handled all play a role in this selection process.
Soft Seals: Ensuring Tight Shut-off
Soft seals, typically made from elastomeric materials like EPDM, Nitrile, or Viton, provide a tight shut-off, preventing even minute leakages. They are ideal for applications requiring zero leakage, such as water treatment or chemical processing. These seals conform to the valve seat, creating a reliable barrier against fluid or gas passage. However, they may have limitations in high-temperature or high-pressure environments.
Metal Seals: Withstanding Harsh Conditions
Metal seals, constructed from materials like stainless steel or bronze, offer superior resistance to high temperatures, pressures, and corrosive media. They are suitable for demanding applications in industries like oil and gas or power generation. Metal seals are known for their durability and ability to withstand extreme conditions. While they may not provide the same level of initial leak tightness as soft seals, they maintain their integrity in harsh environments.
Composite Seals: Combining the Best of Both Worlds
Composite seals combine the advantages of soft and metal seals. They typically feature a metal core for strength and a soft outer layer for tight shut-off. These seals find applications in situations requiring both durability and leak tightness. This design offers a balance between the robust nature of metal seals and the superior sealing capabilities of soft seals. They are often used in applications where both performance characteristics are critical.
Gate Valve Seal Materials: Choosing the Right Material for Optimal Performance
The selection of the appropriate seal material is paramount for ensuring the gate valve’s longevity and performance. Factors to consider when choosing a material include:
- Media Compatibility: The seal material must be compatible with the media flowing through the valve to prevent degradation or swelling. Chemical reactions between the media and the seal can lead to premature failure.
- Temperature Range: The material should withstand the operating temperature range without losing its sealing properties. Extreme temperatures can cause the seal to harden, crack, or lose its elasticity.
- Pressure Rating: The seal must be capable of withstanding the system’s pressure without deformation or failure. Excessive pressure can cause the seal to extrude or rupture.
- Abrasion Resistance: If the media contains abrasive particles, the seal material should exhibit high abrasion resistance to prevent premature wear. Abrasive particles can erode the seal, leading to leakage and reduced performance.
Gate Valve Seal Applications: Where are They Used?
Gate valve seals find applications across a wide range of industries, including:
- Water Treatment: Ensuring leak-free operation in water distribution systems. Preventing leaks in water treatment facilities is crucial for conserving water and maintaining system pressure.
- Oil and Gas: Withstanding harsh conditions in pipelines and refineries. The oil and gas industry demands seals that can handle high pressures, temperatures, and corrosive substances.
- Chemical Processing: Handling corrosive and hazardous chemicals. Chemical processing often involves aggressive chemicals that require specialized seal materials.
- Power Generation: Maintaining high pressures and temperatures in power plants. Power plants rely on gate valve seals to ensure the safe and efficient operation of their systems.
Gate Valve Seal Maintenance: Ensuring Longevity and Reliability
Proper maintenance is essential for extending the life of gate valve seals and ensuring their reliable operation. Regular inspection and replacement of worn seals can prevent costly downtime and leakage. A proactive maintenance approach can significantly reduce the risk of unexpected failures and extend the lifespan of the valves.
Inspection: Identifying Potential Issues
Regularly inspect seals for signs of wear, such as cracks, cuts, or deformation. Early detection of problems can prevent more significant issues down the line. Visual inspections are often sufficient to identify obvious damage, but more thorough inspections may be necessary depending on the application.
Replacement: Timely Intervention
Replace worn seals promptly to maintain the valve’s leak tightness and prevent system failures. Follow manufacturer guidelines for proper replacement procedures. Using the correct tools and techniques during seal replacement is essential to avoid damaging the valve or the new seal.
Gate Valve Seal Troubleshooting: Addressing Common Issues
Despite proper maintenance, gate valve seals may encounter problems. Here are some common issues and their solutions:
- Leakage: Check for wear or damage to the seal. Replace the seal if necessary. Leakage can also be caused by improper installation or debris trapped between the seal and the valve seat.
- Difficult Operation: Inspect for debris or obstructions in the valve. Clean or remove any foreign material. Buildup of scale or other deposits can also hinder the valve’s operation.
- Premature Wear: Ensure the seal material is compatible with the media and operating conditions. Consider using a more durable material if needed. Analyzing the cause of premature wear can help identify the optimal seal material for the specific application.
Gate Valve Seal Selection Guide: A Quick Reference

Feature | Soft Seal | Metal Seal | Composite Seal |
---|---|---|---|
Material | Elastomers (EPDM, Nitrile, Viton) | Stainless Steel, Bronze | Metal core with soft outer layer |
Application | Water treatment, chemical processing | Oil and gas, power generation | Applications requiring both durability and leak tightness |
Temperature | Low to moderate | High | Moderate to high |
Pressure | Low to moderate | High | Moderate to high |
Leakage | Zero | Minimal | Minimal |
Abrasion Resistance | Low | High | Moderate |
Conclusion
Gate valve seals are critical components that ensure the efficient and leak-free operation of gate valves. Selecting the right seal type and material for your specific application is crucial for maximizing performance and longevity. Regular maintenance and prompt troubleshooting can prevent costly downtime and ensure the continued reliability of your gate valve system. Investing in high-quality seals and implementing a robust maintenance program can significantly reduce the total cost of ownership over the valve’s lifespan.
FAQ
What is the primary function of a gate valve seal?
The primary function of a gate valve seal is to prevent leakage of the media flowing through the valve, ensuring efficient and safe operation. A properly functioning seal maintains system pressure and prevents environmental contamination.
How often should gate valve seals be inspected?
The frequency of inspection depends on the application and operating conditions. However, regular inspections, ideally at least annually, are recommended to identify potential issues early on. In harsh environments or critical applications, more frequent inspections may be necessary.
What are the signs of a worn gate valve seal?
Signs of a worn seal include leakage, difficulty in operating the valve, or visible damage to the seal, such as cracks or cuts. Unusual noises or vibrations during valve operation can also indicate a problem with the seal.