Welcome to My Blog!
Before we dive into the content, I’d love for you to join me on my social media platforms where I share more insights, engage with the community, and post updates. Here’s how you can connect with me:
Facebook:https://www.facebook.com/profile.php?id=61563865935136
Now, let’s get started on our journey together. I hope you find the content here insightful, engaging, and valuable.
Introduction
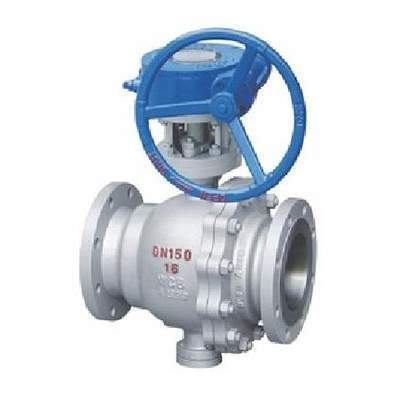
In industries where safety is paramount, such as oil and gas, chemical processing, and power generation, the need for reliable equipment capable of withstanding extreme conditions is critical. Fire safe globe valves are specialized components designed to maintain their integrity and functionality during and after exposure to fire, ensuring the safety of personnel, equipment, and the environment. These valves are essential in systems handling flammable or hazardous fluids, where a failure could lead to catastrophic consequences. This comprehensive guide explores the design, functionality, applications, and standards of fire safe globe valves, providing insights into why they are indispensable in high-risk environments. Whether you’re an engineer, a facility manager, or a procurement specialist, understanding the intricacies of these valves will help you make informed decisions for your operations.
What Are Fire Safe Globe Valves?
Globe valves are linear motion valves known for their spherical body and ability to regulate fluid flow with precision. Fire safe globe valves take this functionality a step further by incorporating design features that ensure they remain operational and leak-free even when exposed to high temperatures during a fire. Unlike standard globe valves, which may fail under extreme heat due to material degradation, fire safe globe valves are engineered with materials and mechanisms that withstand thermal stress. They are typically used in applications where flammable liquids, gases, or other hazardous materials are present, ensuring that the valve maintains a tight seal to prevent leaks that could exacerbate a fire or cause environmental harm.
Key Features of Fire Safe Globe Valves
Fire safe globe valves are distinguished by several critical design elements that enhance their performance in fire-prone environments. These include:
- Metal-to-Metal Seating: Unlike soft-seated valves that rely on elastomeric materials, fire safe globe valves use metal-to-metal seating to ensure a reliable seal even when non-metallic components degrade under high temperatures.
- Graphite Packing: Graphite is commonly used for stem packing due to its ability to withstand temperatures up to 700°C, maintaining a seal around the valve stem to prevent external leakage.
- Thermal Expansion Compensation: Some designs incorporate mechanisms like Belleville washers to compensate for thermal expansion, ensuring the valve disc remains pressed against the seat during a fire.
- Robust Materials: Materials such as stainless steel, carbon steel, or high-performance alloys like Inconel are selected for their ability to resist heat and deformation.
These features collectively ensure that fire safe globe valves can perform their function under extreme conditions, making them a critical component in safety-critical systems.
Why Fire Safe Globe Valves Are Essential
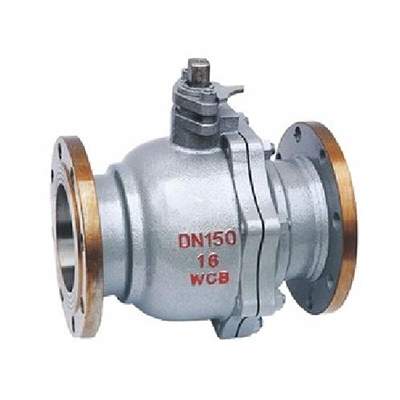
The primary purpose of fire safe globe valves is to prevent the escalation of fire-related incidents by containing hazardous fluids within the piping system. In industries like oil and gas, where flammable hydrocarbons are common, a valve failure during a fire could lead to leaks that fuel the fire or release toxic substances into the environment. Fire safe globe valves are designed to mitigate these risks by maintaining their sealing integrity and operational capability, even when exposed to temperatures between 1400°F and 1800°F for extended periods. Their ability to regulate flow with precision also makes them ideal for applications requiring throttling, such as steam systems or chemical feed lines, where safety and control are paramount.
Applications of Fire Safe Globe Valves
Fire safe globe valves are widely used across various industries due to their reliability in high-risk environments. Some common applications include:
- Oil and Gas: Used in pipelines, refineries, and offshore platforms to control the flow of flammable hydrocarbons, preventing leaks during fire emergencies.
- Chemical Processing: Employed in plants handling volatile substances, where a fire could lead to hazardous leaks if standard valves fail.
- Power Generation: Utilized in fuel and steam lines to ensure safe operation and prevent fire escalation in power plants.
- Pharmaceutical Manufacturing: Applied in processes involving flammable solvents, where fire safe globe valves ensure the safety of personnel and equipment.
- Fire Protection Systems: Incorporated in sprinkler and standpipe systems to regulate water flow while maintaining integrity during fire events.
These applications highlight the versatility and critical role of fire safe globe valves in ensuring safety across diverse industrial settings.
Standards and Certifications for Fire Safe Globe Valves
To ensure reliability, fire safe globe valves must adhere to stringent international standards that govern their design and testing. These standards provide a framework for manufacturers to validate the performance of their valves under fire conditions. Key standards include:
- API 607: Specifies fire test requirements for quarter-turn valves and other valves with nonmetallic seating, ensuring they maintain sealing integrity during and after fire exposure.
- API 6FA: Focuses on fire testing for valves with metal seating, commonly used for globe and gate valves in API 6A and 6D designs.
- ISO 10497: Provides guidelines for fire testing of valves, ensuring they meet performance criteria for tight shutoff and leakage prevention under fire conditions.
- ASME B16.34: Covers pressure-temperature ratings, materials, and testing requirements for valves, including globe valves, ensuring compliance with safety standards.
These standards involve rigorous testing procedures, such as exposing the valve to a controlled fire for 30 minutes, followed by a water quench and operational cycling to verify structural integrity and leak prevention. Compliance with these standards ensures that fire safe globe valves can be trusted in critical applications.
Design Considerations for Fire Safe Globe Valves
The design of fire safe globe valves is a complex process that requires careful consideration of materials, components, and operational requirements. Manufacturers must balance functionality, durability, and cost while ensuring compliance with fire safety standards. Key design considerations include:
Material Selection
The choice of materials is critical to the performance of fire safe globe valves. Common materials include:
- Stainless Steel: Offers excellent corrosion and heat resistance, making it suitable for harsh environments.
- Carbon Steel: Provides durability and strength for high-pressure applications.
- Inconel and Other Alloys: Used in extreme conditions where high temperatures and corrosive fluids are present.
These materials are selected for their ability to maintain structural integrity under thermal stress and resist deformation during a fire.
Sealing Mechanisms
Fire safe globe valves often incorporate dual sealing mechanisms to ensure reliability. The primary seal may use soft materials for normal operation, while a secondary metal-to-metal or graphite-based seal takes over if the primary seal degrades in a fire. This redundancy is critical for preventing both internal and external leakage.
Thermal Expansion Management
During a fire, thermal expansion can cause the valve yoke to expand faster than the stem, potentially lifting the disc off the seat and causing leakage. Advanced designs, such as those using spring-loaded mechanisms or Belleville washers, compensate for this expansion to maintain a tight seal.
Fire Safe Globe Valve Performance Table
The following table outlines key performance characteristics of fire safe globe valves, providing a quick reference for their specifications and capabilities in fire-prone environments.
Feature | Description | Benefit |
---|---|---|
Temperature Resistance | Withstands temperatures up to 1800°F (982°C) during fire testing. | Ensures valve integrity during extreme fire conditions. |
Material Composition | Stainless steel, carbon steel, or high-performance alloys like Inconel. | Provides durability and resistance to thermal deformation. |
Sealing Mechanism | Metal-to-metal seating with graphite packing. | Prevents leakage even when soft seals degrade. |
Pressure Rating | Typically ranges from 150 to 2500 PSI, depending on valve size and design. | Suitable for high-pressure applications in hazardous environments. |
Fire Test Standards | Certified to API 607, API 6FA, or ISO 10497 standards. | Guarantees reliability and compliance with industry safety requirements. |
Valve Size Range | Available in sizes from 1/2″ to 24″ or larger, depending on manufacturer. | Accommodates various piping system requirements. |
Actuation Options | Manual, pneumatic, electric, or hydraulic actuation. | Offers flexibility for different operational needs. |
This table provides a snapshot of the critical attributes that make fire safe globe valves suitable for high-risk applications, helping users select the right valve for their needs.
Installation and Maintenance of Fire Safe Globe Valves
Proper installation and maintenance are essential to ensure the long-term performance of fire safe globe valves. Incorrect installation can compromise the valve’s ability to function during a fire, while neglecting maintenance can lead to wear and reduced reliability.
Installation Guidelines
To install a fire safe globe valve correctly, follow these steps:
- Verify Flow Direction: Check the flow direction indicated on the valve body to ensure proper alignment with the system’s flow.
- Depressurize the System: Ensure the pipeline is depressurized and drained before installation to prevent accidents.
- Secure Connections: Use appropriate end connections (flanged, threaded, or welded) and tighten bolts evenly to avoid damage.
- Test for Leaks: Perform a hydrotest after installation to verify the valve’s integrity under pressure.
Maintenance Best Practices
Regular maintenance extends the lifespan of fire safe globe valves and ensures they perform reliably during emergencies. Key maintenance tasks include:
- Visual Inspections: Regularly check for signs of corrosion, wear, or leakage around the valve body and stem.
- Lubrication: Apply manufacturer-recommended lubricants to the valve stem and moving parts to ensure smooth operation.
- Packing Adjustment: Inspect and adjust the graphite packing to prevent stem leaks, replacing it if necessary.
- Operational Testing: Periodically cycle the valve to confirm it opens and closes smoothly without sticking.
By adhering to these guidelines, users can maximize the reliability and safety of their fire safe globe valves.
Advantages of Using Fire Safe Globe Valves
Fire safe globe valves offer several benefits that make them a preferred choice in high-risk environments:
- Enhanced Safety: Their ability to maintain a tight seal during a fire prevents hazardous leaks, protecting personnel and infrastructure.
- Regulatory Compliance: Certification to standards like API 607 and ISO 10497 ensures compliance with industry safety regulations.
- Operational Reliability: Designed to function under extreme conditions, these valves provide consistent performance in critical applications.
- Versatility: Suitable for a wide range of industries and applications, from oil and gas to pharmaceutical manufacturing.
- Environmental Protection: By preventing leaks, fire safe globe valves minimize the risk of environmental contamination during fire emergencies.
These advantages underscore the importance of selecting fire safe globe valves for systems where safety and reliability are non-negotiable.
Challenges and Limitations of Fire Safe Globe Valves
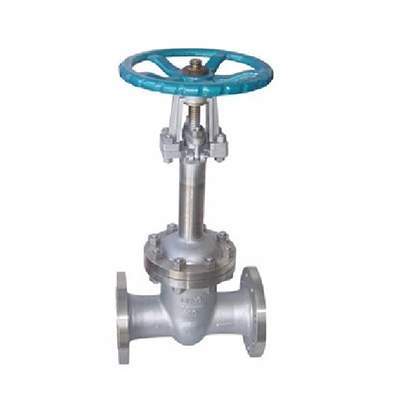
While fire safe globe valves are highly effective, they are not without challenges. Understanding these limitations can help users make informed decisions:
- Pressure Drop: Globe valves inherently cause a higher pressure drop compared to gate or ball valves due to their flow path design, which may not be ideal for applications where minimal head loss is critical.
- Cost: The specialized materials and design features of fire safe globe valves can make them more expensive than standard valves.
- Size Constraints: In very large piping systems, globe valves may not be the most practical choice due to size and weight limitations.
- Maintenance Requirements: The complex design of fire safe globe valves may require more frequent maintenance to ensure optimal performance.
Despite these challenges, the safety benefits of fire safe globe valves often outweigh their limitations in high-risk applications.
Conclusion
Fire safe globe valves are a critical component in ensuring safety and reliability in industries where fire hazards are a constant concern. Their ability to withstand extreme temperatures, maintain sealing integrity, and comply with rigorous standards like API 607 and ISO 10497 makes them indispensable for protecting personnel, equipment, and the environment. By understanding their design, applications, and maintenance requirements, you can make informed decisions to enhance the safety of your operations. For high-quality fire safe globe valves tailored to your needs, contact us today to explore our range of solutions and ensure your systems are prepared for any emergency.
FAQ
What is the difference between a fire safe globe valve and a standard globe valve?
A fire safe globe valve is designed to maintain its sealing integrity and functionality during and after exposure to fire, using materials like graphite packing and metal-to-metal seating. Standard globe valves lack these fire-resistant features and may fail under high temperatures.
How are fire safe globe valves tested?
Fire safe globe valves are tested according to standards like API 607 or API 6FA, which involve exposing the valve to a controlled fire for 30 minutes, followed by a water quench and operational cycling to verify leak prevention and structural integrity.
What industries use fire safe globe valves?
These valves are used in industries such as oil and gas, chemical processing, power generation, pharmaceutical manufacturing, and fire protection systems, where flammable or hazardous fluids are present.