Welcome to My Blog!
Before we dive into the content, I’d love for you to join me on my social media platforms where I share more insights, engage with the community, and post updates. Here’s how you can connect with me:
Facebook:https://www.facebook.com/profile.php?id=61563865935136
Now, let’s get started on our journey together. I hope you find the content here insightful, engaging, and valuable.
Introduction
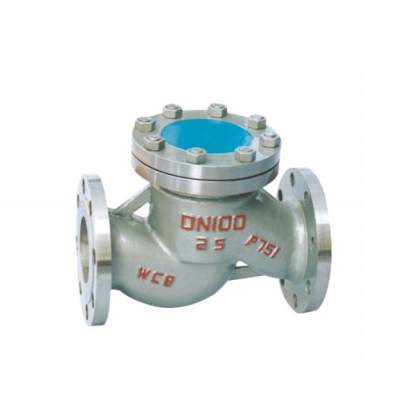
When managing fluid flow in industrial or residential systems, selecting the appropriate components is critical to ensuring efficiency, safety, and longevity. A check flap valve, often referred to as a non-return valve, plays a vital role in preventing backflow, protecting equipment, and maintaining system integrity. These valves are designed to allow fluid to flow in one direction while automatically closing to prevent reverse flow, making them indispensable in applications like water treatment, HVAC systems, and industrial pipelines. However, with various types, materials, and configurations available, choosing the right check flap valve can be daunting. This guide aims to simplify the process by exploring key factors, types, and considerations to help you make an informed decision tailored to your specific needs.
In this blog, we’ll dive into the essentials of check flap valves, covering their functionality, types, and applications. We’ll also provide practical tips to ensure you select a valve that optimizes performance while avoiding common pitfalls. Whether you’re an engineer, a facility manager, or a homeowner, understanding how to choose the right check flap valve is crucial for maintaining a reliable system.
What Is a Check Flap Valve and How Does It Work?
A check flap valve is a mechanical device designed to permit fluid flow in one direction while preventing backflow. The valve features a flap or disc that opens when fluid flows in the intended direction and closes when the flow reverses, typically due to gravity or spring assistance. This simple yet effective mechanism ensures that systems remain protected from contamination, pressure surges, or equipment damage caused by reverse flow.
The operation of a check flap valve is straightforward. When fluid pressure exceeds the valve’s cracking pressure, the flap lifts, allowing flow. If the pressure drops or reverses, the flap closes against the valve seat, creating a seal. This design makes check flap valves ideal for systems where backflow could disrupt operations or cause damage, such as in plumbing, wastewater management, or chemical processing.
Key Components of a Check Flap Valve
To understand how a check flap valve functions, it’s helpful to know its core components. The valve body houses the flap or disc, which is typically made of metal, plastic, or rubber, depending on the application. The hinge or pivot allows the flap to move freely, while the valve seat ensures a tight seal when closed. Some designs include a spring to enhance closing speed or a counterweight to adjust the valve’s sensitivity to flow changes. These components work together to ensure reliable performance under varying conditions.
Types of Check Flap Valves for Different Applications
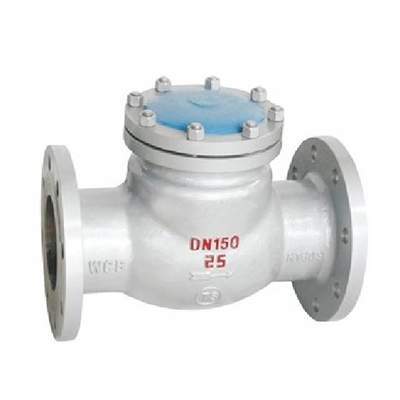
Check flap valves come in several designs, each suited to specific applications. Understanding the types available can help you select the one that best meets your system’s requirements.
Swing Check Flap Valves
Swing check flap valves feature a disc that swings open on a hinge or pivot when fluid flows in the desired direction. When flow reverses, the disc swings back to close the valve. These valves are commonly used in water and wastewater systems due to their simplicity and low maintenance requirements. They perform well in applications with low to moderate flow rates and are often found in large-diameter pipelines.
Wafer Check Flap Valves
Wafer check flap valves are compact and lightweight, designed to fit between two flanges in a pipeline. Their slim profile makes them ideal for space-constrained installations, such as HVAC systems or industrial processes. These valves often use a dual-plate design, where two flaps close independently, offering faster response times and reduced water hammer.
Tilting Disc Check Flap Valves
Tilting disc check flap valves have a disc that tilts rather than swings, providing a quicker closure and reducing the risk of slamming. These valves are suitable for high-pressure systems or applications with rapid flow changes, such as in oil and gas pipelines. Their design minimizes wear and extends service life in demanding environments.
Spring-Assisted Check Flap Valves
Spring-assisted check flap valves incorporate a spring to force the flap closed more quickly, making them ideal for systems with frequent flow reversals. These valves are often used in chemical processing or irrigation systems, where rapid closure is essential to prevent backflow-related issues.
Factors to Consider When Choosing a Check Flap Valve
Selecting the right check flap valve requires careful consideration of several factors to ensure compatibility with your system. Below are key aspects to evaluate.
Fluid Type and Compatibility
The type of fluid flowing through your system—whether water, oil, gas, or chemicals—greatly influences the valve material. For example, corrosive fluids like seawater or chemicals require materials like stainless steel or PVC to prevent degradation. Understanding your fluid’s properties, such as viscosity and temperature, ensures the valve can withstand operational conditions without failing.
System Pressure and Flow Rate
The pressure and flow rate of your system determine the valve’s size and design. High-pressure systems may require a tilting disc or spring-assisted check flap valve to handle rapid flow changes, while low-pressure systems might work well with a swing check valve. Always check the valve’s pressure rating to ensure it matches your system’s requirements.
Installation Space and Orientation
The available space and orientation of your pipeline can limit your valve options. Wafer check flap valves are ideal for tight spaces, while swing check valves may require more room due to their larger disc movement. Additionally, some valves function better in horizontal or vertical orientations, so confirm the valve’s compatibility with your setup.
Maintenance and Durability Needs
Consider the maintenance requirements and expected lifespan of the valve. In harsh environments, such as wastewater treatment plants, a durable valve with minimal maintenance needs is preferable. Opt for materials and designs that resist wear and corrosion to reduce long-term costs.
Comparison Table of Check Flap Valve Features
To help you visualize the differences between check flap valve types, the table below outlines key characteristics of swing, wafer, tilting disc, and spring-assisted valves. This comparison focuses on their design, applications, and advantages.
Valve Type | Design Features | Best Applications | Advantages | Limitations |
---|---|---|---|---|
Swing Check Flap Valve | Single disc swings on a hinge | Water, wastewater, low-flow systems | Simple, low maintenance | Slower closure, risk of water hammer |
Wafer Check Flap Valve | Dual-plate, compact design | HVAC, space-constrained systems | Lightweight, fast response | Limited to smaller pipe sizes |
Tilting Disc Valve | Disc tilts for quick closure | High-pressure, oil/gas pipelines | Reduced slamming, durable | Higher cost, complex design |
Spring-Assisted Valve | Spring aids rapid flap closure | Chemical processing, irrigation | Fast closure, reliable in dynamic flows | Requires periodic spring maintenance |
This table provides a snapshot of each valve type’s strengths and limitations, helping you narrow down your options based on your system’s needs.
Installation Tips for Optimal Check Flap Valve Performance
Proper installation is critical to maximizing the performance and lifespan of a check flap valve. Incorrect installation can lead to leaks, premature wear, or system inefficiencies. Here are some tips to ensure a successful setup.
Ensure Proper Alignment
Misalignment during installation can cause the flap to stick or fail to seal properly. Ensure the valve is correctly aligned with the pipeline and that flanges or connections are secure. For vertical installations, verify that the valve is designed to operate in that orientation to prevent operational issues.
Check for Debris Before Installation
Debris or contaminants in the pipeline can damage the valve or impair its function. Flush the system thoroughly before installing the check flap valve to remove any particles that could interfere with the flap’s movement or sealing capability.
Verify Flow Direction
Every check flap valve has a designated flow direction, typically indicated by an arrow on the valve body. Installing the valve in the wrong direction will render it ineffective, allowing backflow. Double-check the flow direction during installation to avoid costly mistakes.
Common Mistakes to Avoid When Selecting a Check Flap Valve
Choosing the wrong check flap valve can lead to system inefficiencies, increased maintenance costs, or even catastrophic failures. Here are common pitfalls to avoid.
Ignoring Fluid Compatibility
Selecting a valve material incompatible with the fluid can result in corrosion or degradation. For instance, using a standard steel valve in a corrosive environment like a chemical plant can lead to rapid failure. Always match the valve material to the fluid’s chemical properties.
Oversizing or Undersizing the Valve
Choosing a valve that’s too large or too small for your system can cause inefficiencies. An oversized valve may not open fully, reducing flow capacity, while an undersized valve can create excessive pressure drops. Calculate the correct valve size based on your system’s flow rate and pipe diameter.
Neglecting Maintenance Requirements
Some check flap valves require regular maintenance, such as spring replacements or cleaning, to function optimally. Failing to account for these needs can lead to unexpected downtime. Choose a valve with maintenance requirements that align with your operational capabilities.
Maintenance and Troubleshooting for Check Flap Valves
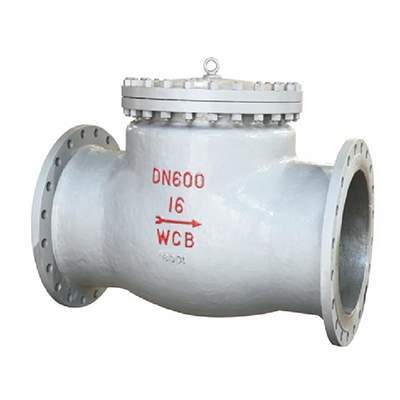
Regular maintenance ensures that your check flap valve operates efficiently and has a long service life. Here are some maintenance and troubleshooting tips.
Routine Inspection and Cleaning
Periodically inspect the valve for signs of wear, corrosion, or debris buildup. Clean the flap and seat to ensure a proper seal and smooth operation. For spring-assisted valves, check the spring tension and replace it if it shows signs of fatigue.
Addressing Common Issues
If the valve fails to close properly, it may be due to debris, a damaged flap, or incorrect installation. Inspect the valve and pipeline for blockages and verify that the valve is correctly oriented. If the valve slams shut, consider a tilting disc or spring-assisted design to reduce water hammer.
When to Replace a Check Flap Valve
If the valve shows signs of significant wear, such as cracks in the flap or body, or if it no longer seals effectively, it’s time for a replacement. Regular inspections can help you identify when a valve is nearing the end of its service life, allowing you to plan replacements proactively.
Conclusion
Choosing the right check flap valve is essential for ensuring the efficiency, safety, and longevity of your fluid management system. By understanding the types of valves available, considering factors like fluid compatibility, pressure, and installation requirements, and avoiding common mistakes, you can select a valve that meets your specific needs. Regular maintenance and proper installation further enhance performance, reducing the risk of costly downtime or system failures. Whether you’re managing a large industrial pipeline or a small residential system, the right check flap valve can make all the difference.
Ready to find the perfect check flap valve for your system? Contact us today to explore our range of high-quality valves and get expert guidance tailored to your needs!
FAQ
What is the main purpose of a check flap valve?
A check flap valve prevents backflow in a piping system, ensuring fluid flows in one direction only. This protects equipment and maintains system efficiency in applications like water treatment or industrial processes.
Can a check flap valve be installed vertically?
Yes, many check flap valves can be installed vertically, but it’s essential to choose a valve designed for vertical orientation. Swing check valves, for example, may require specific configurations to function correctly in vertical pipelines.
What materials are best for a check flap valve?
The best material depends on the fluid and environment. Stainless steel or bronze is ideal for corrosive fluids, while PVC or plastic suits non-corrosive applications like water or irrigation systems.